Fundamentos de optimización en calderas
Debido a la amplia utilización de calderas para satisfacer las demandas térmicas en la industria, es preciso conocer las áreas de optimización y ahorro energético en este proceso para aplicarlo con la mayor eficiencia posible
Leopoldo Guzmán / Imágenes: cortesía del autor
La producción de vapor a través de una caldera es uno de los métodos más utilizados para generación de energía térmica, ya que el vapor permite entregar calor y energía simultáneamente hacia un proceso, el mismo se genera a partir de agua y no se degrada con el uso o la temperatura. No obstante, resulta indispensable conocer las diferentes dificultades que se pueden presentar en la operación de las calderas con la finalidad de utilizarlas eficientemente debido al incremento en el costo económico de los combustibles, así como contribuir con los esfuerzos globales de reducción de emisiones contaminantes y adicionalmente poder satisfacer los requerimientos de la industria para la optimización de sus procesos.
Problemas básicos en el interior de calderas de vapor
En el interior de una caldera las principales causas que provocan una deficiente transferencia de energía y una reducción en la eficiencia térmica se deben a los fenómenos de incrustación, corrosión, arrastres y depósitos sólidos; los cuales surgen principalmente debido a deficiencias en el tratamiento físico-químico del agua, así como un inadecuado control sobre las purgas.
Tratamiento de agua
Los diferentes tipos de tratamiento generalmente utilizados son en función de los resultados que se pretenden obtener, siendo principalmente los procesos de ablandamiento o suavizado con el propósito de evitar incrustaciones, desmineralización para la reducción del nivel de sólidos totales disueltos y de aeración del agua de alimentación que tiene como objetivo remover el oxígeno disuelto y disminuir la probabilidad de corrosión.
Purgas de fondo y superficie
Adicional al tratamiento del agua es necesario implementar un procedimiento para remover periódicamente los sólidos asentados a través de una válvula instalada en la parte inferior de la caldera, lo cual se conoce como purga de fondo, la cual en caso de ser correctamente automatizada minimiza el desperdicio de agua previamente tratada y calentada, así como una reducción en el riesgo de incrustaciones y disminución de envío de agua caliente al drenaje.
Para calderas de gran capacidad, adicionalmente, es indispensable asegurar la calidad del agua dentro de la misma a través de una purga de superficie o continua que consiste en el control constante de la cantidad de sólidos disueltos en ella. Dentro de las ventajas de un sistema automático de purga de superficie tendremos una mejor calidad del vapor generado, ahorro del agua tratada químicamente, menor frecuencia de paros por mantenimiento y control continuo del nivel de sólidos totales disueltos.
Una adecuada selección del tratamiento en función de las propiedades químicas del agua y un correcto control de las purgas traen consigo beneficios de ahorro energético y reducción de problemas en el interior de las calderas.
Recuperación de energía
En las calderas de vapor es posible aplicar técnicas que nos permitan retornar los condensados hacia la misma y adicionalmente usar las altas temperaturas de los gases de combustión que se liberan hacia la atmósfera para realizar un intercambio de calor, con el propósito de aprovechar esa energía y disminuir el consumo del combustible.
Economizador
Debido a las elevadas temperaturas de humos se puede lograr una recuperación de calor de los gases de combustión, circulando el agua de alimentación de la caldera a través de un intercambiador de energía llamado economizador, el cual será ubicado en la chimenea de la misma, permitiendo que dichos gases cedan su calor al agua de alimentación aumentando su temperatura, siendo necesario menor consumo de combustible para la producción de vapor.
Retorno de condensados
En la mayoría de las instalaciones de calderas es recomendable el aprovechamiento del condensado (vapor que ha cambiado de estado a fase líquida), el cual trae consigo menores costos de tratamiento, ya que se retorna agua previamente tratada y con bajo contenido de sólidos disueltos totales, así como una reducción de consumo y ahorro de energía al utilizar agua de alimentación a mayor temperatura.
Tanto el uso del economizador y la instalación para el retorno de condensados dependerán de diversos factores propios de la aplicación y las condiciones de operación de los procesos; los cuales en caso de ser favorables para su uso permiten tener periodos de amortización breves en función de la inversión requerida.

Relación Aire-Combustible
El proceso de combustión en el quemador de una caldera se produce a través de una reacción química entre el oxígeno (O2, obtenido regularmente del aire del ambiente) y un material oxidable o combustible, que en conjunto de un elemento de ignición se obtiene una flama en el quemador.
Una vez teniendo una flama presente, tanto el aire (O2) y el combustible deben mantener una relación adecuada al ser mezclados entre sí con el propósito de lograr una combustión completa; donde se obtenga el mayor aprovechamiento del poder calorífico del combustible, bajas emisiones y una mejor transferencia de energía. No obstante, es probable que al depender de elementos mecánicos para el control de mezcla aire-combustible la combustión pueda contener grandes cantidades de exceso de aire lo que implica una menor eficiencia de combustión, o por el contrario se tenga una combustión incompleta que propicia la producción de monóxido de carbono (CO), presencia de hollín el cual en cantidades acumuladas actúa como aislante térmico que desfavorece el intercambio de calor, que en conjunto denota desperdicio de combustible.
Con base en esto se debe buscar un equilibrio entre el rendimiento y las emisiones contaminantes a través del control adecuado de la mezcla aire-combustible.
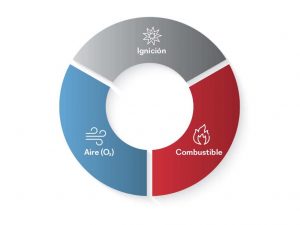
Posicionamiento Paralelo Electrónico para mezcla Aire-Combustible
Consiste en una técnica de control electrónico para la mezcla aire-combustible con servo-motores independientes y de alta precisión, para lograr y mantener una combustión completa en todos los puntos de operación del quemador, desde la posición de mínima modulación, o fuego bajo, hasta el punto de máxima modulación, o fuego alto. Al aplicar esta técnica de control se puede alcanzar la mayor eficiencia de combustión que el quemador permita, favoreciendo una menor producción de hollín, así como una disminución del punto de bajo fuego del quemador para disminuir el consumo de combustible en condiciones de baja demanda; lo cual en conjunto mejora el uso del quemador y se consigue ahorro de combustible.
Energía eléctrica
En calderas de gran capacidad el elemento que representa el mayor consumo de energía eléctrica es el motor de aire de combustión, debido a que en condiciones nominales de operación el mismo se encontrará trabajando a plena carga consumiendo el cien por ciento de la energía a la que fue diseñado, aunque el porcentaje de utilización del mismo en función de la cantidad de aire requerida para la combustión pudiera ser mucho menor, existiendo un potencial de ahorro energético.
Variador de Frecuencia para motor de aire de combustión
Para poder utilizar de manera eficiente el motor de aire de combustión es posible aplicar un Variador de Frecuencia (VFD), que permitirá variar las revoluciones por minuto (RPM) del mismo y de esa forma entregar la cantidad de aire exacta que se requiere para la combustión sin necesidad de utilizar el motor a un mayor porcentaje de carga de lo que realmente se requiere. Al aplicar esto en conjunto con el sistema de posicionamiento paralelo electrónico se pueden tener los siguientes beneficios:
- Ahorro de energía eléctrica
- Regulación precisa del flujo de aire requerido para la combustión
- Reducción del desgaste del motor
- Disminución de contaminación auditiva por ruido
Puntos adicionales de mejora
Adicional a los temas ya mencionados pueden considerarse los siguientes como puntos de valoración y evaluación para buscar una mejora del proceso de generación y distribución de vapor:
- En las líneas de distribución de vapor: fugas, trampas de vapor dañadas, deficiente aislamiento en tuberías, válvulas y depósitos
- Pérdidas de calor en las paredes de la caldera
- Inadecuado diseño o dimensionamiento de la caldera en función del proceso
- Mala calibración del sistema de control de combustión
- Prácticas incorrectas y vicios de operación
Emisiones
Uno de los beneficios adyacentes de lograr una combustión completa en el quemador es la reducción de emisiones contaminantes a la atmósfera, para lo cual es posible aplicar técnicas adicionales para el control de las mismas.
Auto-carburación
Consiste en incorporar al sistema de control de relación aire-combustible un sensor en la salida de gases de combustión para obtener una retroalimentación de las emisiones en tiempo real, de esa manera el sistema de control podrá realizar ajustes en la curva de combustión de manera automática en caso de existir variaciones del poder calorífico del combustible o en la concentración de oxígeno en el aire.
Reducción de NOx
Para buscar bajos niveles de NOx (óxido de nitrógeno) es preciso reducir la temperatura de la flama, que no supere los 1 300 °C, y de los gases de combustión, para lo cual se pueden considerar los siguientes métodos:
- Correcta selección de un quemador que proporcionará el nivel concreto de emisiones requeridas
- Recirculación externa de humos
- Elementos mecánicos insertados en el hogar
- Tratamiento químico; inyección de amoniaco u otros procedimientos
Para mayor referencia de las normatividades aplicables en México y los niveles máximos permisibles de emisión de los equipos de combustión de calentamiento indirecto y su medición, se puede consultar la NOM-085-SEMARNAT.
Continuidad de operación
Aunado a los temas de ahorro energético y reducción de emisiones, es importante considerar que la caldera forma parte de un proceso en el cual es indispensable evitar paros no planeados, reducir los tiempos muertos en caso de existir una interrupción no deseada del proceso y buscar datos que permitan mejorar los KPIs (indicadores clave de rendimiento).
Inteligencia de Proceso de Combustión
A través de las herramientas de comunicación y gestión de datos que existen actualmente es posible integrar los instrumentos de seguridad, control y medición de la caldera para lograr un análisis avanzado de detección y prevención de problemas, los cuales pueden integrarse junto con los datos del proceso para establecer estrategias de mantenimiento y de respuesta a fallos, así como realizar una evaluación del desempeño de activos y equipos, lo cual permitirá prepararse para futuros incidentes que puedan poner en riesgo la operación del negocio.
La gestión de datos en conjunto de análisis e inteligencia de proceso, nos brinda posibilidades de mejora en la toma de decisiones para la optimización de recursos y activos.
Leopoldo Guzmán
Ingeniero en Electrónica y Comunicaciones por el Instituto Tecnológico de Estudios Superiores de Monterrey. Cuenta con 13 años de experiencia en sistemas de control de combustión, participando en el desarrollo de automatización y soluciones de ahorro energético para la industria y principales fabricantes de equipo original (OEM) de combustión residencial e industrial en México. Actualmente, es gerente de ingeniería y proyectos para Honeywell Thermal Solutions México.